CASE STUDY:
BRONZE
STEEL INDUSTRY
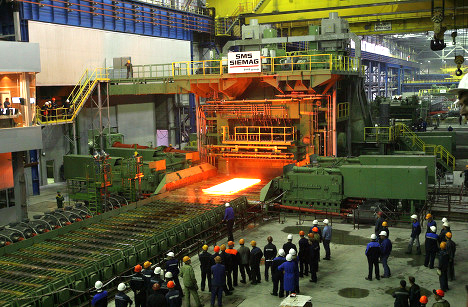
BACKGROUND
Steel is the world's most important engineering material due to high strength relative to weight and price. Steel is produced in many forms - from thin sheets to coarse supporting bridge beams.
Most of the steel manufacturing consists of products to be processed and further refined. This is usually done by hot rolling to form various products such as plates, strips, rods, profiles, wires and pipes. Sometimes, additional cold rolling is applied for example in the manufacturing of thin sheet metal.
Rolling mills can consist of thousands of rolls and are constantly running around the clock, year-round. In order to maintain tolerances and surface finish, maintenance of the rolls is an absolute necessity, and the rolls are therefore grinded regularly to prevent that the steel is processed with defective rolls, which would have very negative consequences.
In the event of processing with a defective roll, the rolled steel can, at best, simply be processed again, but to lift steel in and out of the mill takes time and involves an extra cost as the process time will be longer. In the more negative case steel rolled with full force. This can destroy both the rolling mill roll packages and peripherals. This means that a total of twenty different rollers must be replaced. A time-consuming work that takes more than one shift to perform. This leads to large production time losses as well as increased total production expenses as downtime costs are around $10,000 per hour. Of course, the security aspect is another major concern, as a defective roll in the worst case can be the cause of an accident.
PROBLEM
The grinding of rolls is performed with a rotating grinding wheel which is moved horizontally back and forth along the roll.
The grinding process generates heating of the roll to extreme temperatures and the roll must be cooled to avoid overheating. The coolant fluid also removes the dust generated during the grinding.
To ensure that the rolls, which can be very large and heavy, do not bend from the abrasive forces and their own weight grinding supports are used. Grinding supports are usually made of bronze because it is a softer material than steel and can’t destroy the steel rolls during grinding. The regular bronze grinding supports wear out quickly by the steel rolls and by the residual dust generated in the grinding process. Therefore, the grinding supports are exchanged at regular intervals.
The steel manufacturing plant Outokumpu in Avesta, Sweden wear out 8 grinding supports per machine per week. Outokumpu has two machines in the Avesta. Another example is the German steel manufacturer Thyssen with several plants, at the Krefeld plant at full production wear out 18 grinding supports every three days and at the Benrath plant 12 grinding supports every three days. The difference in how frequently the grinding supports are exchanged in the different plants depends on the geometry of the grinding supports.
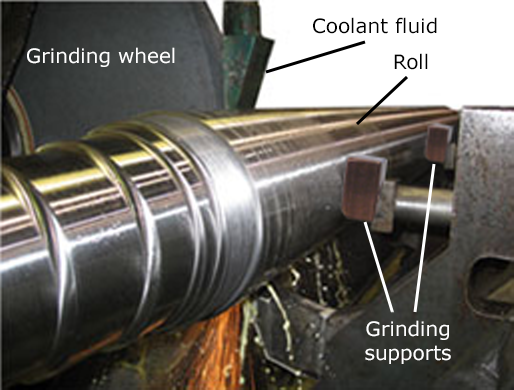
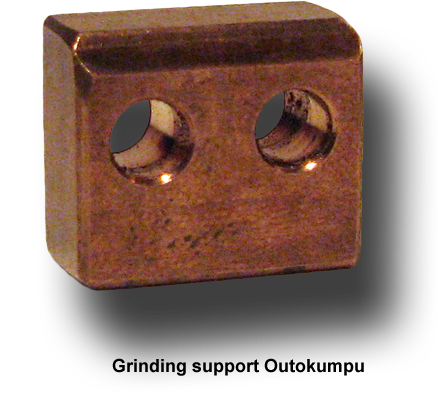
SOLUTION
Grinding supports made of bronze modified by Toroidal graphene last considerably longer than conventional bronze grinding supports.
The improved functionality, thanks to our far more durable Toroidal graphene/bronze composite material represents great savings especially in the process-time, where downtime is reduced to less than 20%.
500%
IMPROVEMENT
IN
ABRASIVE
WEAR
RESISTANCE
Grinding supports made of bronze modified by Toroidal graphene have been tested both by Outokumpu in Avesta, Sweden and by Thyssen at their plant in Krefeld, Germany.
We produced grinding support prototypes both for Outokumpu and Thyssen for testing purposes. The initial tests have showed very good results, with the grinding supports made of bronze modified by Toroidal graphene lasting at least five times as long as the conventional grinding supports with the same lubrication (coolant fluid) and in the same environment.
LET'S GET
TOGETHER.
If you believe that we may have a technology that could be of benefit to your company ...
or if you just want to chat …